PDC ATTRIBUTES
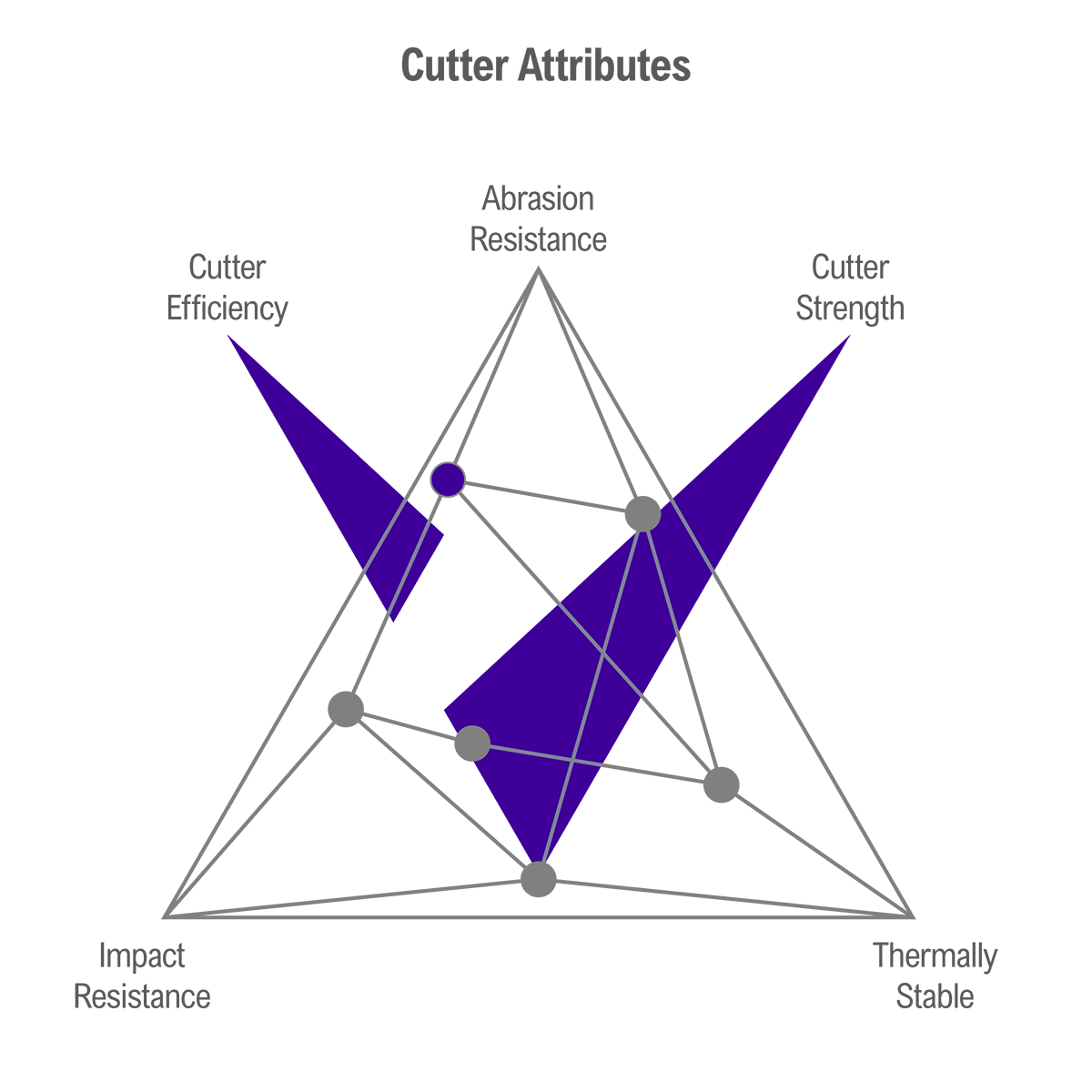
VENOM™ Cutter Technology
- VENOM™ Sales Flyer
- 9-7/8” Drillout Delivers One-Bit Record Performance
- New Fastest 16” Vertical Section in KUWAIT
- New Fastest 16” Deviated Section in ABU DHABI, U.A.E
- Superior Performance Delivered in Challenging 17-1/2” Section – UK Central North Sea
- 200% ROP enhancement in Sinian System/Formation – Onshore China
- New PDC Benchmark Set in Delta Mahakam Area, East Kalimantan
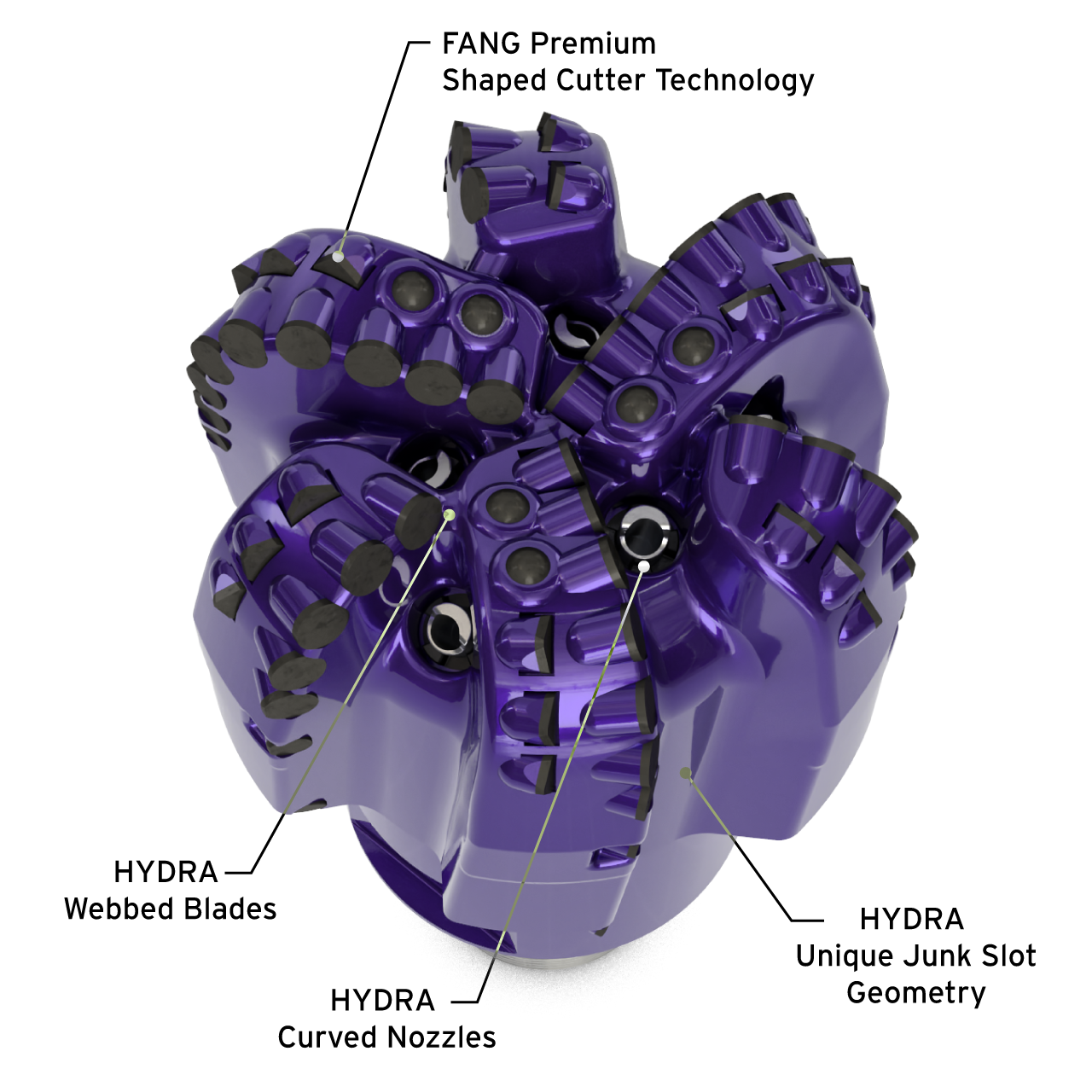
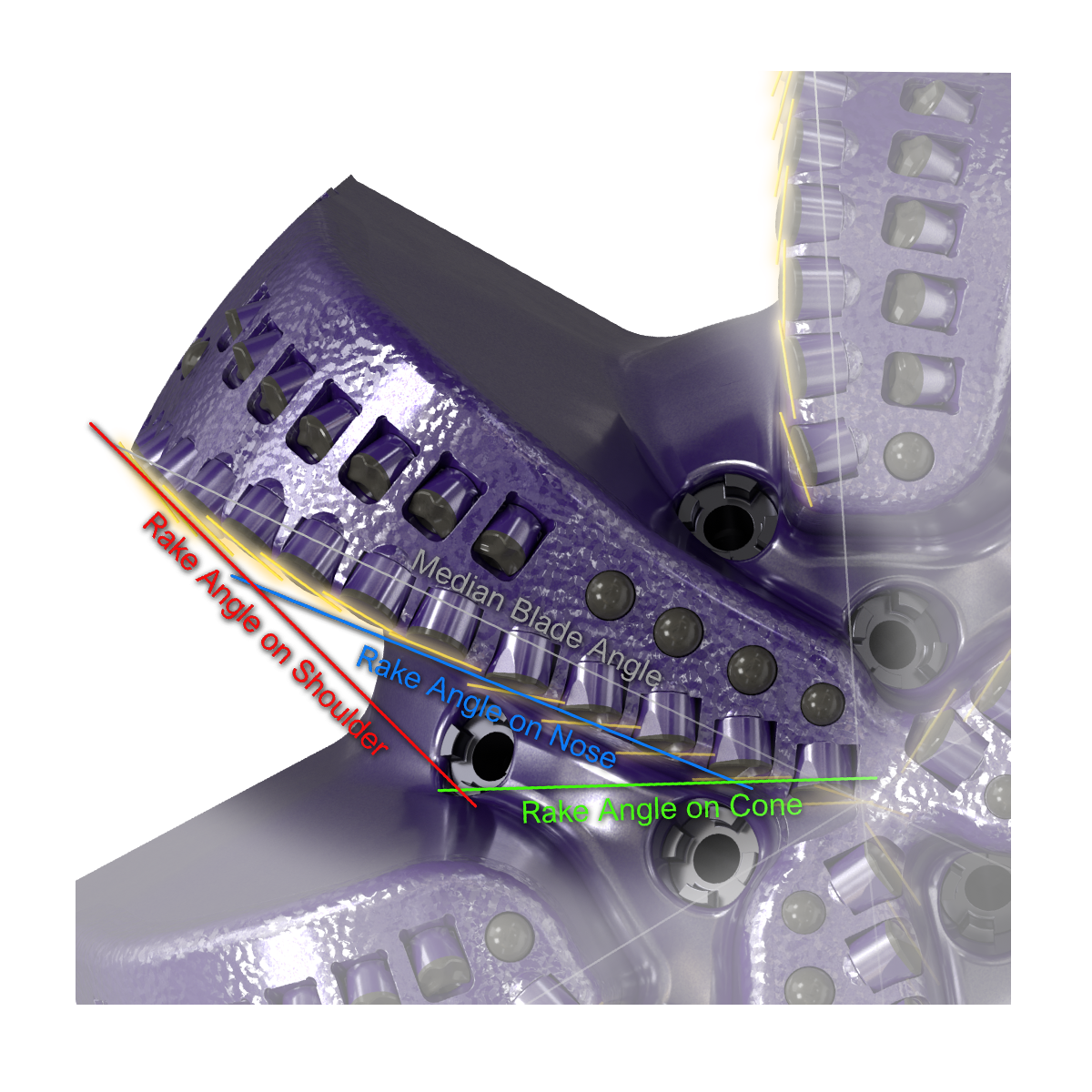